An Unbiased View of Alcast Company
Table of ContentsFascination About Alcast CompanyThe Definitive Guide to Alcast CompanyThe 6-Minute Rule for Alcast CompanyThe Alcast Company StatementsExcitement About Alcast CompanyAlcast Company Can Be Fun For Everyone
Chemical Contrast of Cast Aluminum Alloys Silicon promotes castability by minimizing the alloy's melting temperature level and enhancing fluidity throughout casting. Additionally, silicon contributes to the alloy's strength and put on resistance, making it valuable in applications where durability is essential, such as vehicle components and engine parts.It additionally boosts the machinability of the alloy, making it much easier to process into ended up items. This way, iron adds to the overall workability of aluminum alloys. Copper raises electric conductivity, making it useful in electric applications. It additionally improves rust resistance and contributes to the alloy's overall toughness.
Manganese adds to the stamina of aluminum alloys and boosts workability. Magnesium is a lightweight element that supplies toughness and effect resistance to light weight aluminum alloys.
Facts About Alcast Company Uncovered
It allows the manufacturing of lightweight components with outstanding mechanical buildings. Zinc improves the castability of aluminum alloys and aids regulate the solidification process throughout casting. It improves the alloy's strength and solidity. It is often located in applications where detailed shapes and great details are required, such as decorative castings and particular auto components.
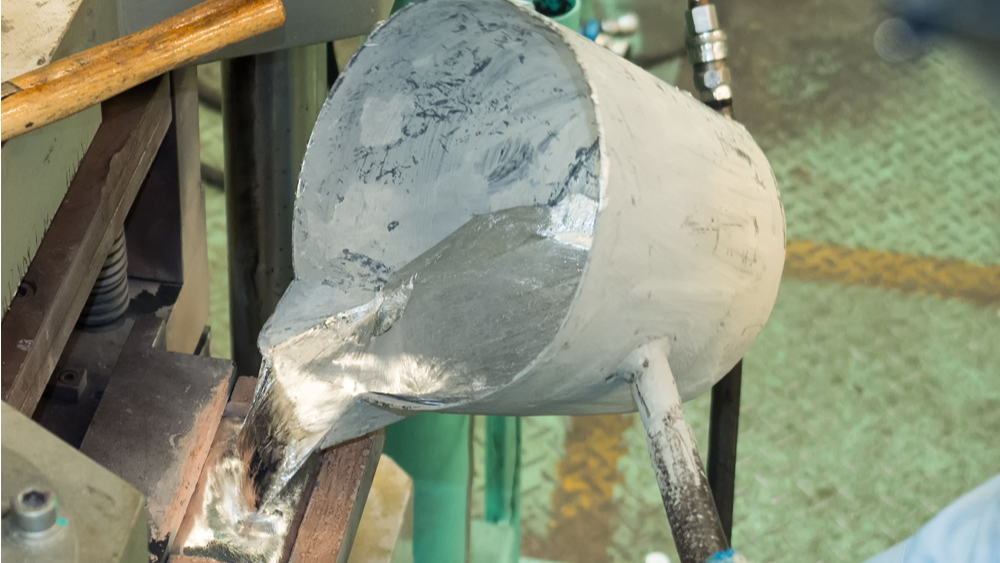
The primary thermal conductivity, tensile strength, return stamina, and elongation vary. Amongst the above alloys, A356 has the greatest thermal conductivity, and A380 and ADC12 have the cheapest.
The Ultimate Guide To Alcast Company
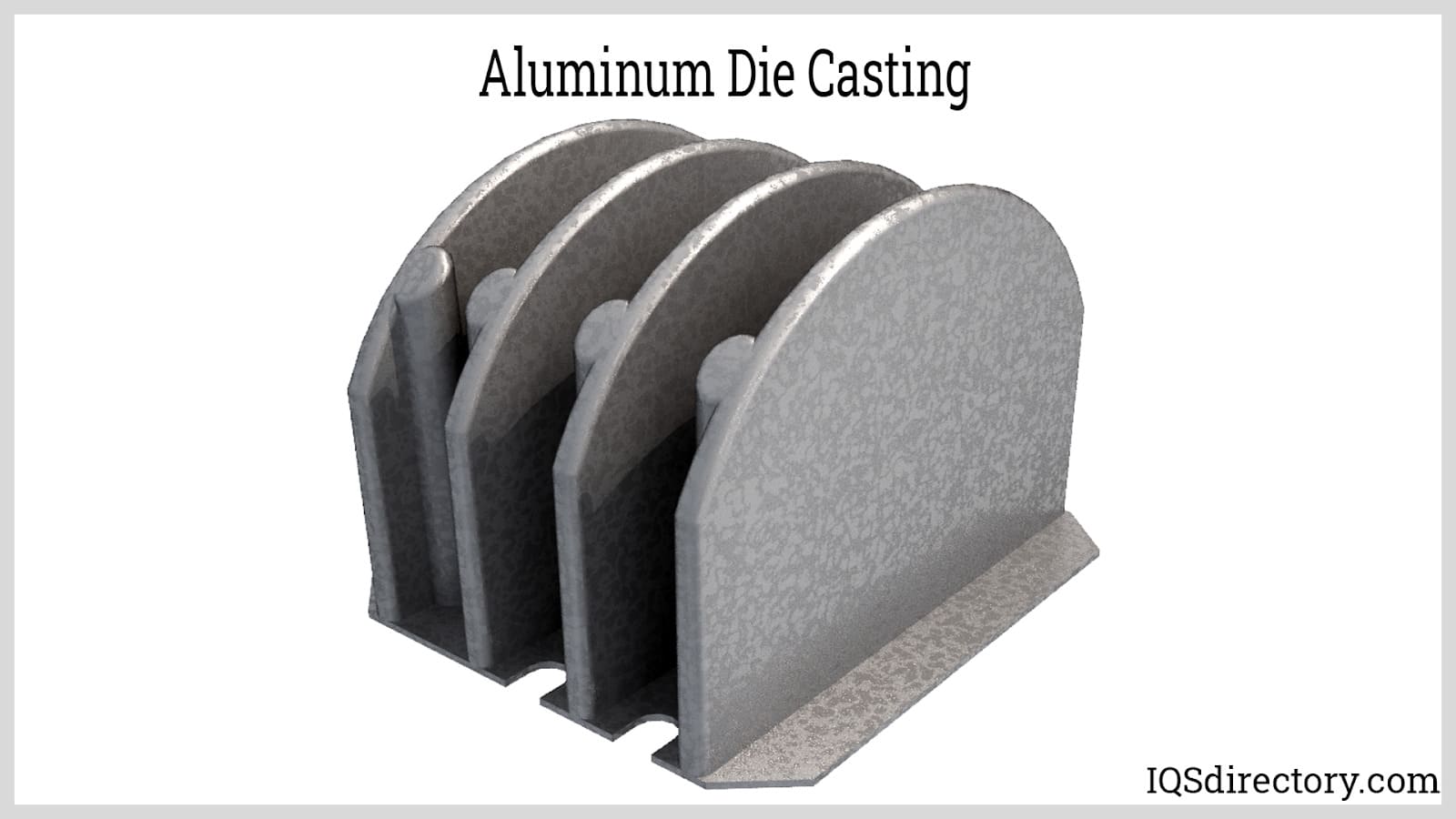
In precision spreading, 6063 is appropriate for applications where complex geometries and premium surface area finishes are extremely important. Examples include telecommunication rooms, where the alloy's exceptional formability enables smooth and cosmetically pleasing styles while maintaining structural honesty. In a similar way, in the Lights Solutions market, precision-cast 6063 elements create stylish and efficient lighting components that need detailed shapes and excellent thermal efficiency.
It brings about a better surface area finish and much better deterioration resistance in A360. Moreover, the A360 shows superior elongation, making it optimal for complicated and thin-walled parts. In accuracy spreading applications, A360 is fit for industries such as Customer Electronic Devices, Telecommunication, and Power Tools. Its enhanced fluidity enables intricate, high-precision components like smart device housings and communication tool real estates.
How Alcast Company can Save You Time, Stress, and Money.
Its one-of-a-kind buildings make A360 a useful option for precision spreading in these sectors, enhancing item sturdiness and quality. Light weight aluminum alloy 380, or A380, is a commonly used spreading alloy with several distinct features. It uses excellent castability, making it a suitable choice for accuracy spreading. A380 shows excellent fluidness when molten, guaranteeing complex and detailed mold and mildews are accurately recreated.
In accuracy casting, aluminum 413 beams in the Customer Electronic Devices and Power Equipment industries. This alloy's premium corrosion resistance makes try this out it a superb choice for outdoor applications, ensuring long-lasting, sturdy items in the stated sectors.
The Greatest Guide To Alcast Company
The light weight aluminum alloy you select will significantly impact both the casting procedure and the homes of the final item. Because of this, you have to make your choice very carefully and take an educated approach.
Determining the most suitable aluminum alloy for your application will suggest considering a wide variety of features. The initial classification addresses alloy attributes that impact the manufacturing procedure.
The Basic Principles Of Alcast Company
The alloy you pick for die spreading directly influences numerous aspects of the spreading process, like how simple the alloy is to work with and if it is prone to casting defects. Hot splitting, likewise understood as solidification fracturing, is a common die spreading problem for aluminum alloys that can cause inner or surface-level rips or fractures.
Specific aluminum alloys are much more susceptible to hot breaking than others, and your option should consider this. Another usual issue found in the die casting of aluminum is die soldering, which is when the cast adheres to the die wall surfaces and makes ejection hard. It can damage both the cast and the die, so you need to try to find alloys with high anti-soldering residential properties.
Corrosion resistance, which is currently a significant attribute of aluminum, can vary considerably from alloy to alloy and is a necessary particular to consider depending upon the environmental problems your item will certainly be exposed to (Foundry). Put on resistance is one more residential or commercial property frequently looked for in light weight aluminum items and can separate some alloys